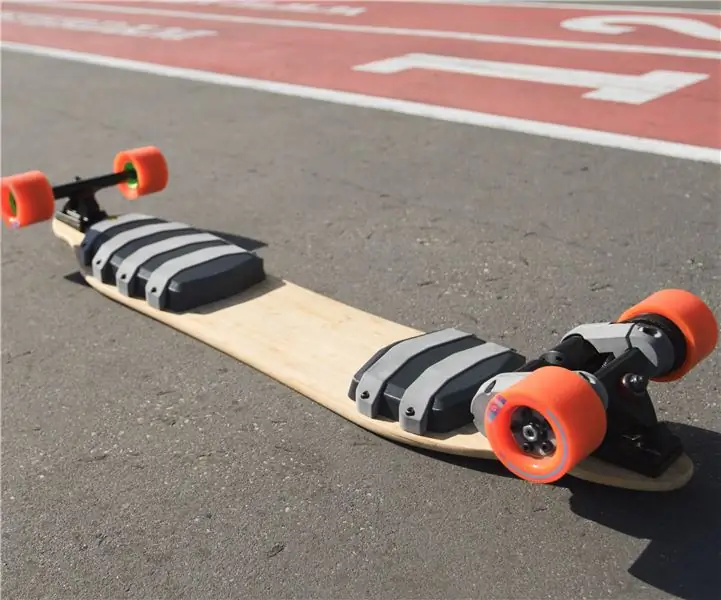
Kazalo:
2025 Avtor: John Day | [email protected]. Nazadnje spremenjeno: 2025-01-23 15:09
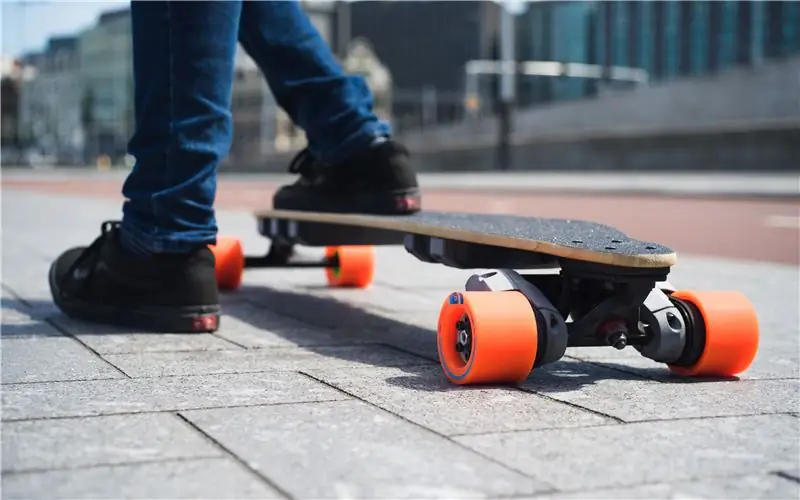
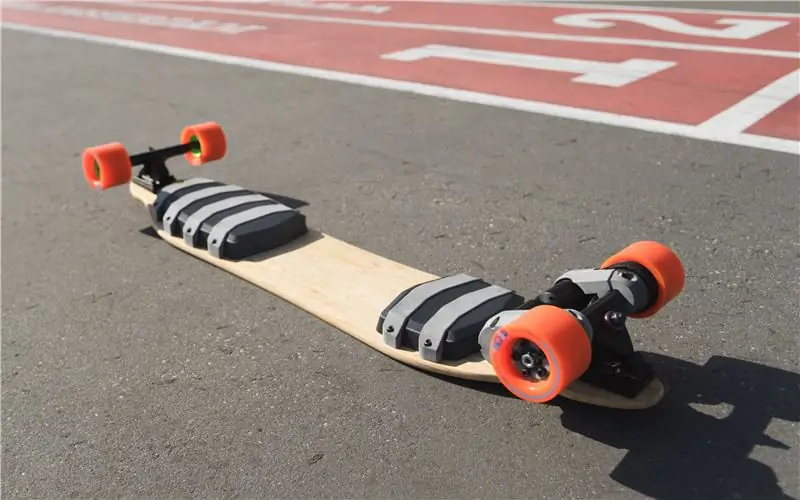
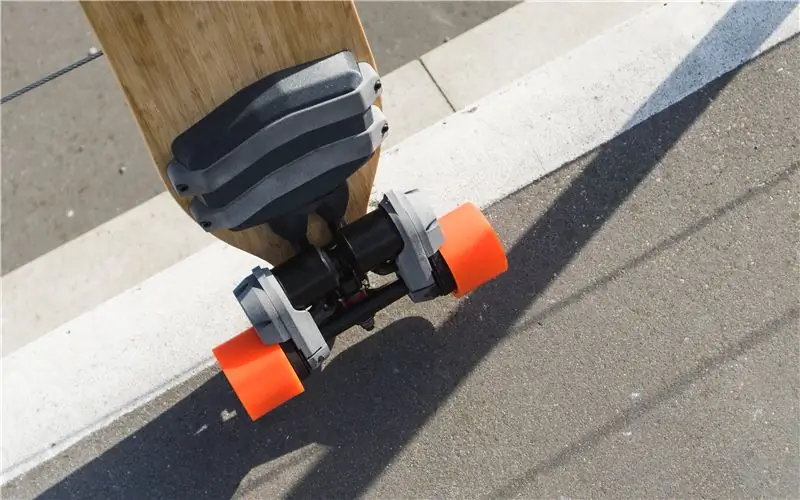
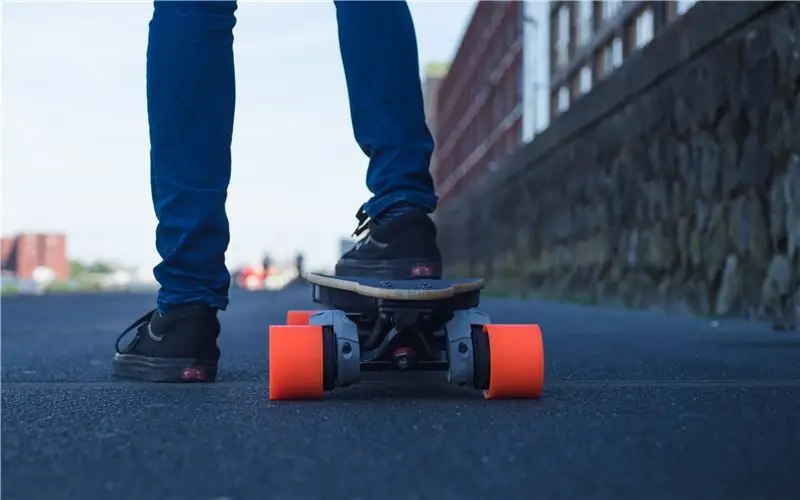
Ta Instructable je pregled postopka izdelave Fusion E-Board-a, ki sem ga oblikoval in izdelal med delom v 3D Hubih. Projekt je bil naročen za promocijo nove tehnologije HP Multi-Jet Fusion, ki jo ponujajo 3D Hubs, ter za prikaz več tehnologij 3D tiskanja in njihove učinkovite kombinacije.
Oblikoval sem in izdelal električno motorizirano longboard, ki se lahko uporablja za kratka do zmerna potovanja ali v kombinaciji z javnim prevozom, da ponudi veliko širši doseg. Ima visoko končno hitrost, je zelo vodljiv in ga je enostavno prenašati, ko ga ne uporabljate.
1. korak: Postopek oblikovanja
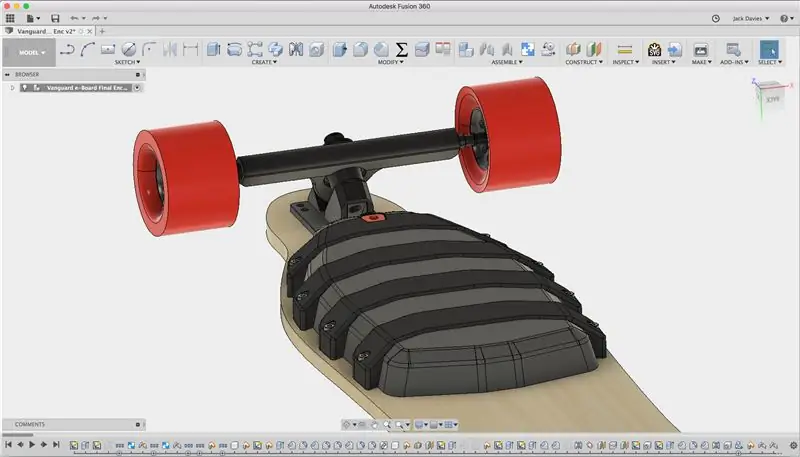
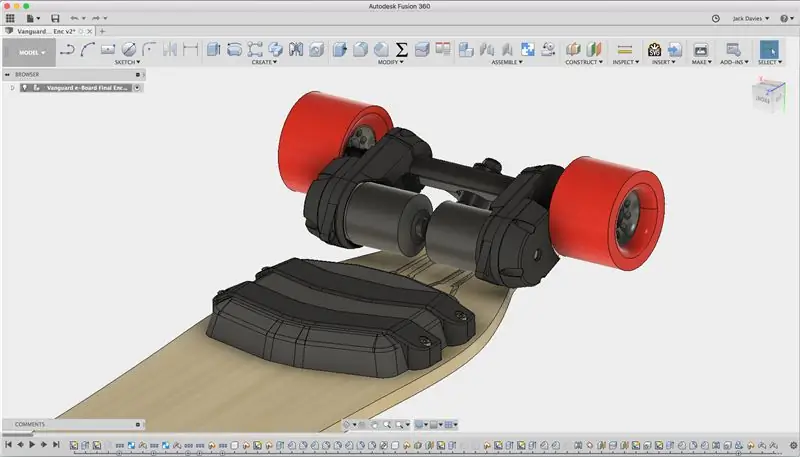
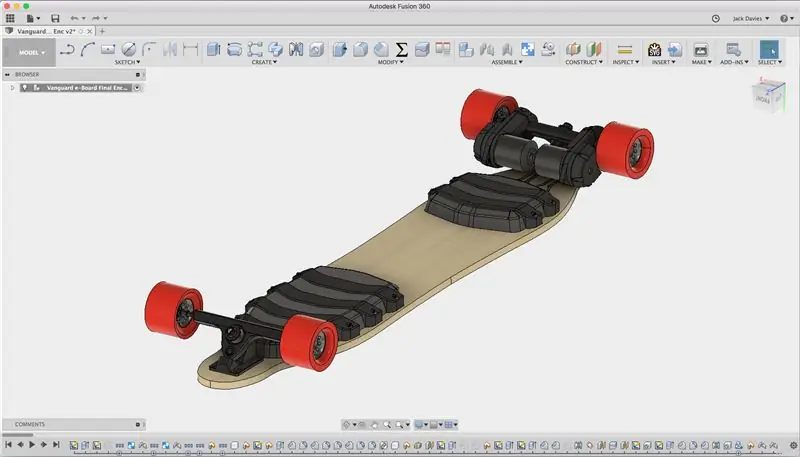
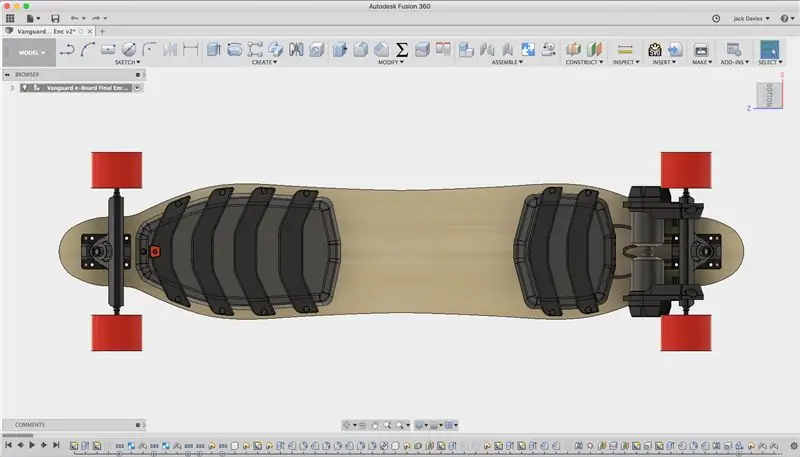
Projekt sem začel z opredelitvijo glavnih standardnih komponent longboard; tovornjaki, paluba in kolesa. To so bili deli police, zato sem jih uporabil kot izhodišče pri oblikovanju. Prva faza je bila načrtovanje pogonskega sklopa, ki vključuje nosilce motorja, nastavitev zobnikov in nekatere spremembe tovornjakov. Velikost in položaj nosilcev motorja bi določala velikost in lokacijo ohišij, zato je bilo pomembno, da se to najprej zaključi. Izračunala sem želeno največjo hitrost in navor, kar mi je nato omogočilo izbiro motorjev in baterije za ploščo. Izračunano je bilo tudi prestavno razmerje in izbrane velikosti jermenic ter dolžina pogonskega jermena. To mi je omogočilo, da sem določil pravilno velikost nosilcev motorja, kar je zagotovilo dobro napeti jermen.
Naslednja stopnja je bila oblikovanje ohišij za baterijo in regulator hitrosti (ESC). Izbrani krov je pretežno sestavljen iz bambusa, zato je precej prilagodljiv in se močno upogiba na sredini. To ima prednosti, ker je udobno za vožnjo, saj absorbira neravnine na cesti in jih ne prenese na kolesarja. Vendar to tudi pomeni, da je za namestitev baterije in elektronike potrebno deljeno ohišje, saj se ohišje v celotni dolžini ne more upogniti s ploščo in bi med delovanjem prišlo v stik s tlemi. Elektronski regulatorji hitrosti (ESC) so bili zaradi električnih omejitev nameščeni najbližje motorjem. Ker so motorji pritrjeni s tovornjaki, se položaj med zavoji spreminja, zato je bilo treba ohišje oblikovati tako, da omogoča odmik motorjev.
Akumulatorski sistem je bil nameščen na drugem koncu palube in v njem je bila elektronika, povezana z napajanjem. To vključuje baterijo, sestavljeno iz 20 litij -ionskih celic 18650, sistem za upravljanje baterije, stikalo za vklop/izklop in vtičnico za polnjenje.
Za celoten proces načrtovanja sem uporabil Autodesk Fusion360, ta programska oprema mi je omogočila hitro modeliranje komponent znotraj glavnega sklopa, kar je znatno pospešilo čas razvoja. Uporabil sem tudi simulacijske funkcije v Fusion360, da zagotovim, da bodo deli dovolj močni, zlasti nosilci motorja. To mi je omogočilo, da sem dejansko zmanjšal velikost nosilcev, saj sem lahko preveril zahteve glede trdnosti in upogibanja ter odstranil material, hkrati pa ohranil ustrezen varnostni faktor. Po končanem postopku oblikovanja je bilo posamezne dele zelo enostavno izvoziti za 3D tiskanje.
2. korak: pogonski sklop
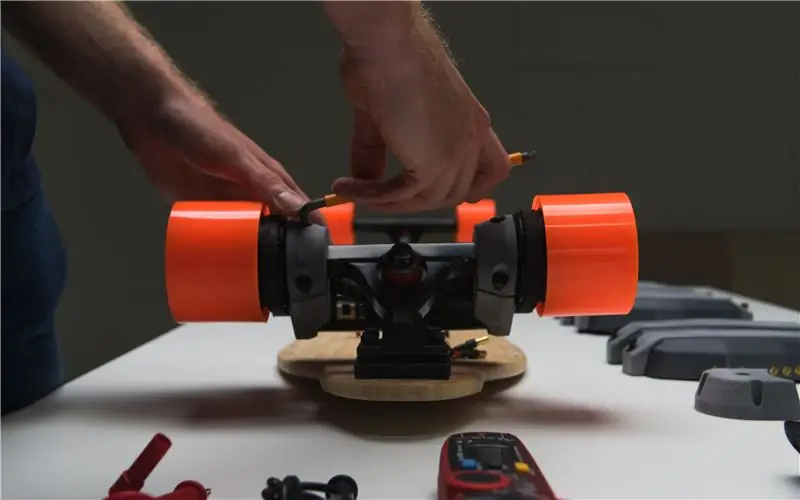
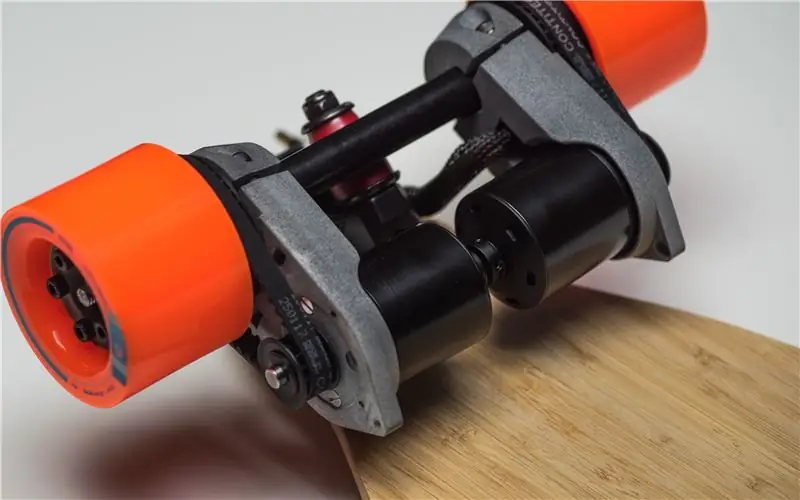
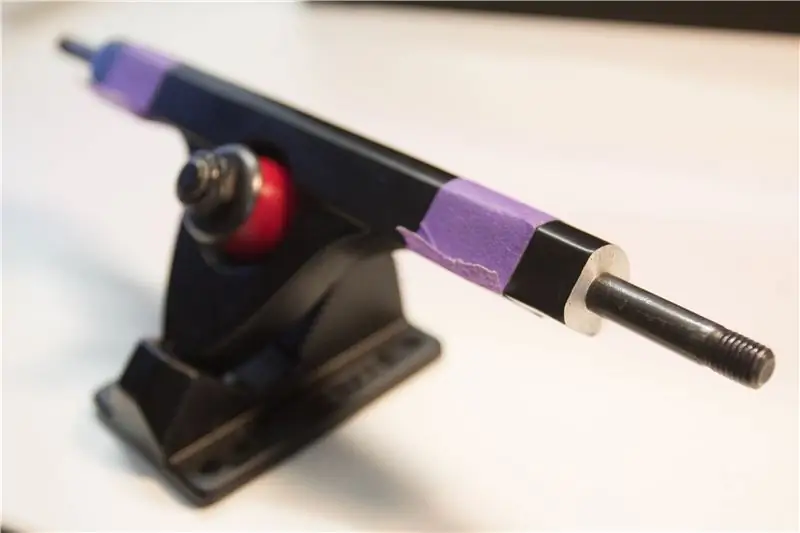
Najprej sem dokončal izdelavo pogonskega sklopa, da sem zagotovil ustrezno zračnost za ohišje elektronike. Za uporabo sem izbral tovornjake Calibre, saj imajo kvadratni profil, ki je bil kot nalašč za vpenjanje nosilcev motorja. Vendar je bila os nekoliko prekratka, da bi lahko dva motorja uporabljali na istem tovornjaku, zato sem to moral podaljšati, da so se kolesa lahko prilegala.
To sem dosegel tako, da sem odrezal nekaj aluminijastih obešalnikov za tovornjake in izpostavil več jeklene osi. Nato sem odrezal večino osi in pustil približno 10 mm, ki sem jih nato lahko navojil z matrico M8.
Nato bi lahko privili spojko in ji dodali še eno navojno os, s čimer bi osi učinkovito podaljšali. Za trajno pritrditev spojke in nove osi sem uporabil zadrževalno maso Loctite 648, da se med uporabo ne bi odvil. To je omogočilo, da sta dva motorja nameščena na tovornjak in zagotovila veliko prostora za kolesa.
Pogonski sklop je bil v prvi vrsti natisnjen s tehnologijo HP Multi-Jet Fusion, da se zagotovi togost in trdnost med velikimi pospeški in zaviranjem, kamor bi se prenesle največje sile.
Za blokiranje zadnjih koles je bil zasnovan poseben jermenica, ki je bila nato z jermenom motorja povezana s pasom HTD 5M. Za zaščito sklopa jermenice je bil dodan 3D natisnjen pokrov.
3. korak: Ohišja reber
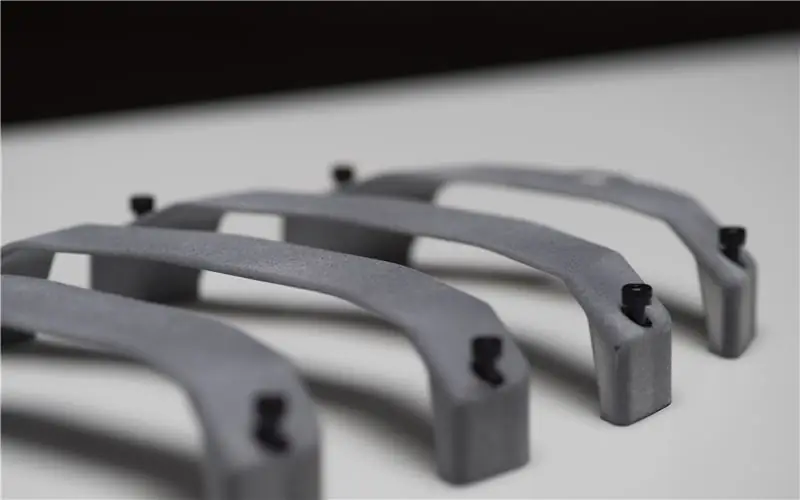
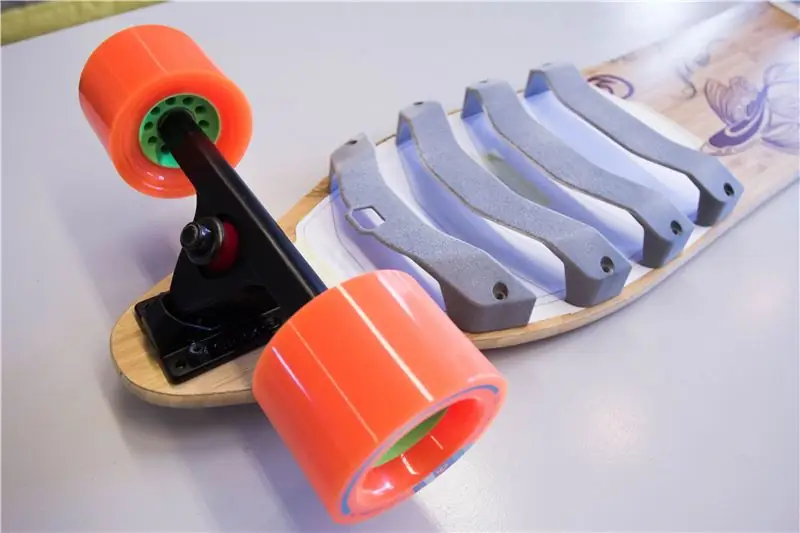
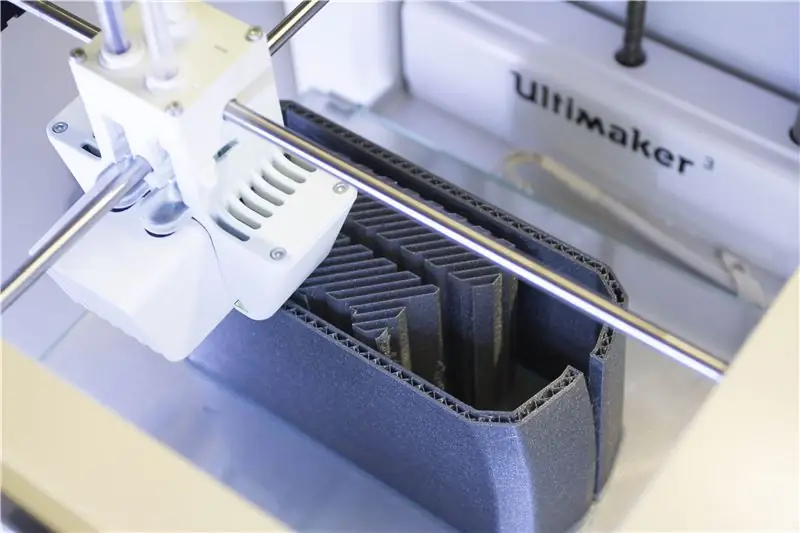
Ena glavnih oblikovalskih odločitev, ki sem jih sprejel, je bila ločitev ohišij, kar je povzročilo čist videz in omogočilo, da je fleksibilna paluba delovala brez dodatne togosti ohišij. Želel sem predstaviti funkcionalne vidike tehnologije HP Multi Jet Fusion, zato sem se odločil, da FDM natisnem glavno ohišje ohišij, kar je zmanjšalo stroške, in nato uporabil HP -jeve dele za podporo in pritrditev na krov. To je prineslo zanimivo estetiko, hkrati pa je bilo tudi zelo funkcionalno.
Tiskana ohišja iz FDM so bila razdeljena na polovico, kar je pomagalo pri tiskanju, saj je bilo mogoče podporni material odstraniti z zunanje površine. Razcepljena črta je bila skrbno nameščena, da se zagotovi, da jo del HP skrije, ko je pritrjena na ploščo. Dodane so bile luknje za priključke motorja in na njih so zlepljeni pozlačeni konektorji krogel
V bambusov krov so bili vstavljeni navojni vložki, ki so ohišja pritrdili na desko, in jih pobrusili skupaj s površino plošče, da bi zagotovili, da med krovom in ohišjem ni vrzeli.
4. korak: Elektronika
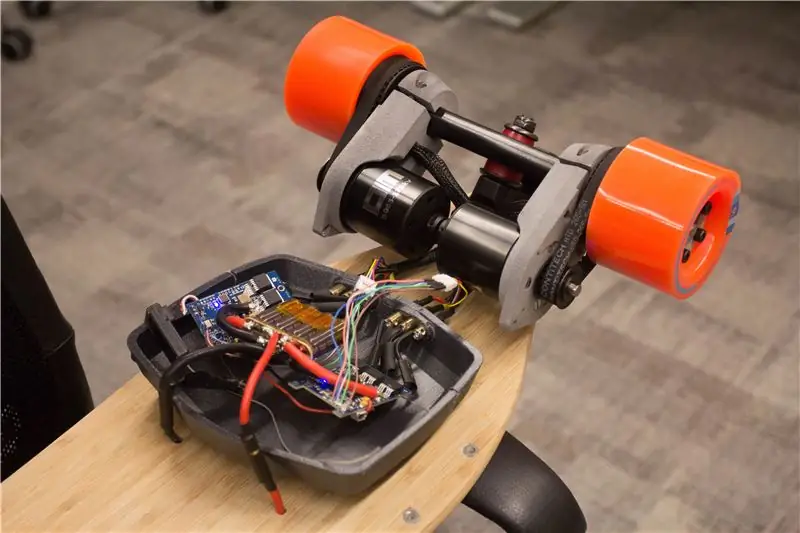
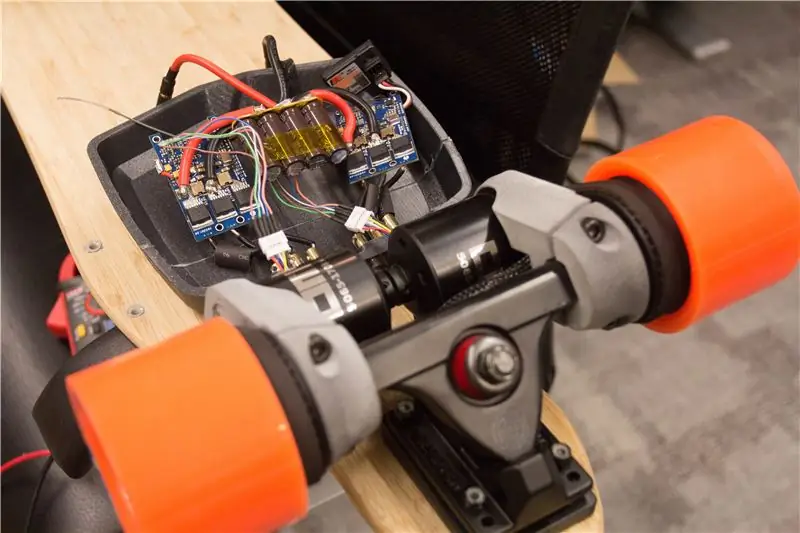
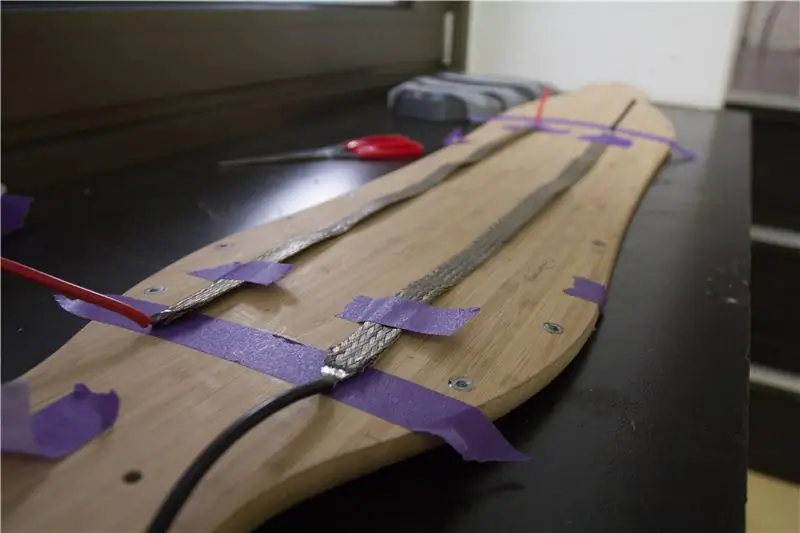
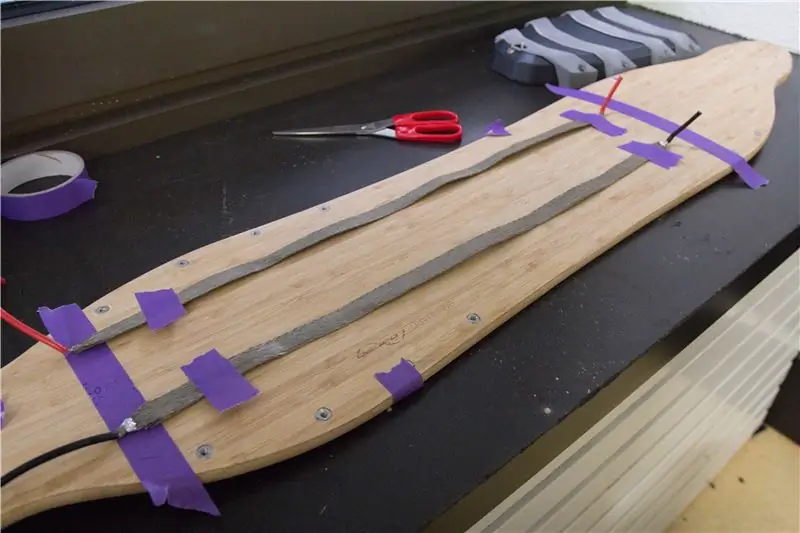
Elektronika je bila skrbno izbrana, da se zagotovi, da je plošča zmogljiva, a tudi intuitivna za uporabo. Ta plošča bi lahko bila potencialno nevarna, če bi prišlo do okvar, zato je zanesljivost zelo pomemben dejavnik.
Baterijski paket je sestavljen iz 20 posameznih litij-ionskih celic 18650, ki so točkovno varjene skupaj, da tvorijo paket 42V. 2 celici sta varjeni vzporedno in 10 zaporedno; celice, ki sem jih uporabil, so bile Sony VTC6. Za varjenje nikljevih jezičkov sem uporabil točkovni varilnik, ki nastane pri pakiranju, saj spajkanje ustvarja preveč toplote, ki lahko poškoduje celico.
Moč iz ohišja akumulatorja je bila prenesena v škatlo krmilnika hitrosti z ravnim pletenim kablom, ki je potekal tik pod oprijemalnim trakom na zgornji strani krova. To je omogočilo "skrivanje" kablov in odpravilo potrebo po napeljavi kablov na spodnji strani, kar bi bilo videti grdo.
Ker gre za dvojno motorno ploščo, sta za neodvisno krmiljenje vsakega motorja potrebna dva regulatorja hitrosti. Za to gradnjo sem uporabil krmilnik hitrosti VESC, ki je posebej zasnovan za električne rolke, zaradi česar je zelo zanesljiv za to uporabo.
Uporabljeni motorji so 170kv 5065 out-runnerjev, ki lahko proizvedejo po 2200W, kar je velika moč za to ploščo. S trenutno nastavitvijo zobnikov je največja hitrost plošč okoli 35MPH in se zelo hitro pospeši.
Zadnja faza je bila izdelava daljinskega upravljalnika za nadzor plošče. Zaradi lažjega delovanja je bil prednostnejši brezžični sistem. Vendar je bilo pomembno zagotoviti visoko zanesljivost prenosa, saj bi lahko padec komunikacije povzročil resne varnostne težave, zlasti pri visokih hitrostih. Po preizkusu nekaj protokolov radijskega prenosa sem se odločil, da bo radijska frekvenca 2,4 GHz najbolj zanesljiva za ta projekt. Uporabil sem avtomobilski oddajnik RC, vendar sem s prenosom elektronike v majhno ročno ohišje, ki je bilo 3D natisnjeno, znatno zmanjšal velikost.
5. korak: Končana tabla in promocijski video
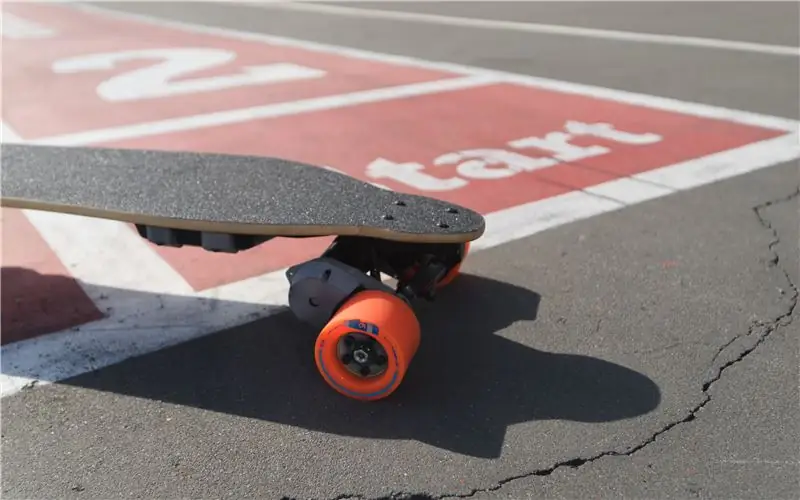
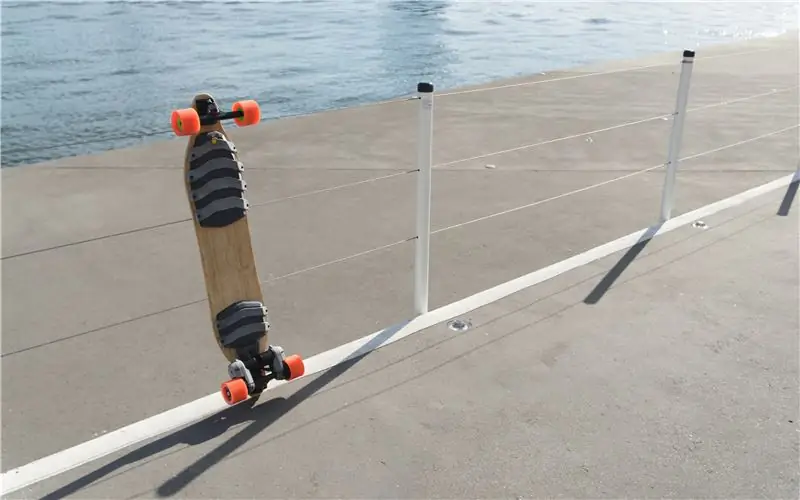
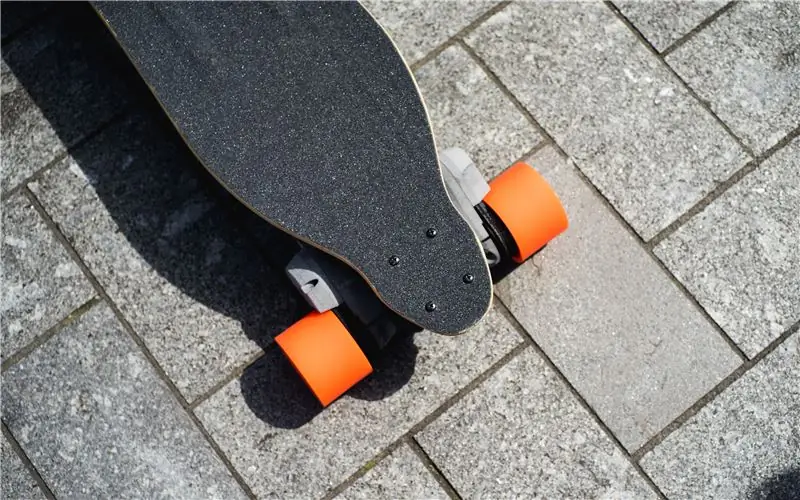
Projekt je zdaj končan! Ustvarili smo čudovit videoposnetek plošče v akciji, ki si jo lahko ogledate spodaj. Najlepša hvala 3D Hubom, ki so mi omogočili ta projekt - preverite jih tukaj za vse vaše potrebe po 3D tiskanju! 3dhubs.com
Priporočena:
3D natisnjena LED svetilka za razpoloženje: 15 korakov (s slikami)
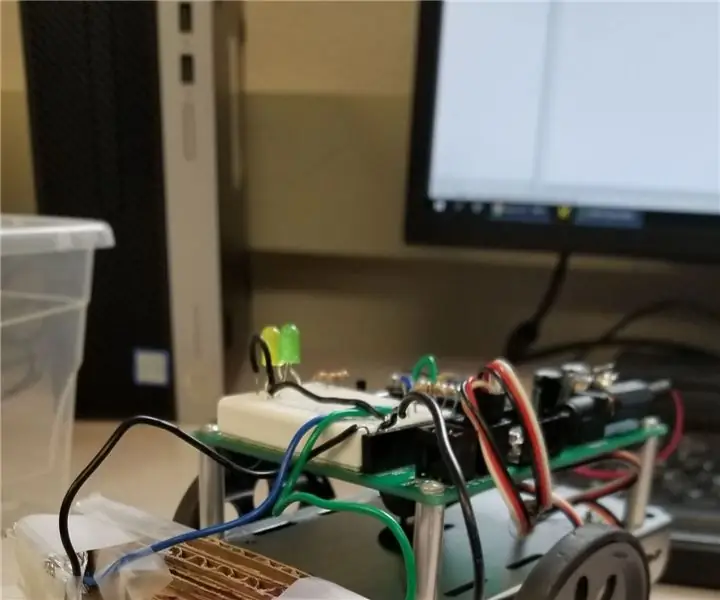
3D tiskana LED svetilka za razpoloženje: Vedno sem bil navdušen nad svetilkami, zato sem imel možnost združiti 3D tiskanje in Arduino z LED, kar sem si moral prizadevati. Koncept je zelo preprost in rezultat je eden najbolj zadovoljivih vizualnih izkušnje, ki jih lahko podate
Speedboard: Električna rolka: 5 korakov
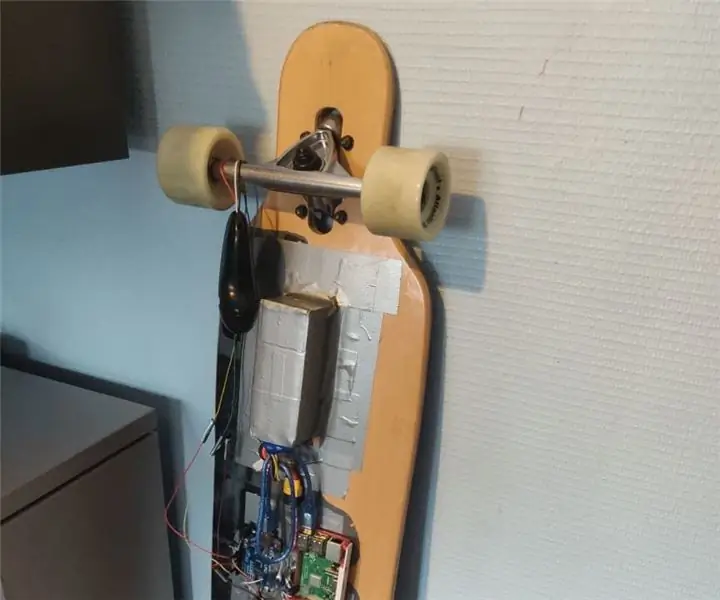
Speedboard: Električna rolka: Pozdravljeni! Sem študent MCT College iz Howesta v Belgiji. Danes vam bom dal korak za korakom navodila, kako narediti električno rolko z malinovim pi in arduinom. Za ta projekt me je navdihnil slavni youtuber z imenom Casey Neistat .
Lahka grafitna rolka: 6 korakov (s slikami)
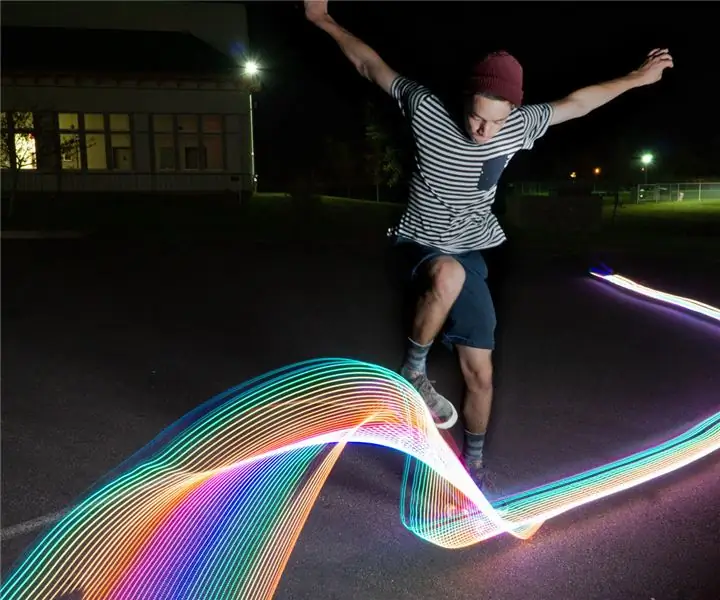
Light Graffiti Skateboard: V preteklosti sem delal lahke grafite in vedno najdem rezultate in obdelavo tako zabavno. Želel sem narediti še korak naprej in delati na svojih ustvarjalnih sposobnostih za izdelavo lahke rolke za grafite. Evo, kako sem to naredil
Električna rolka, občutljiva na pritisk: 7 korakov
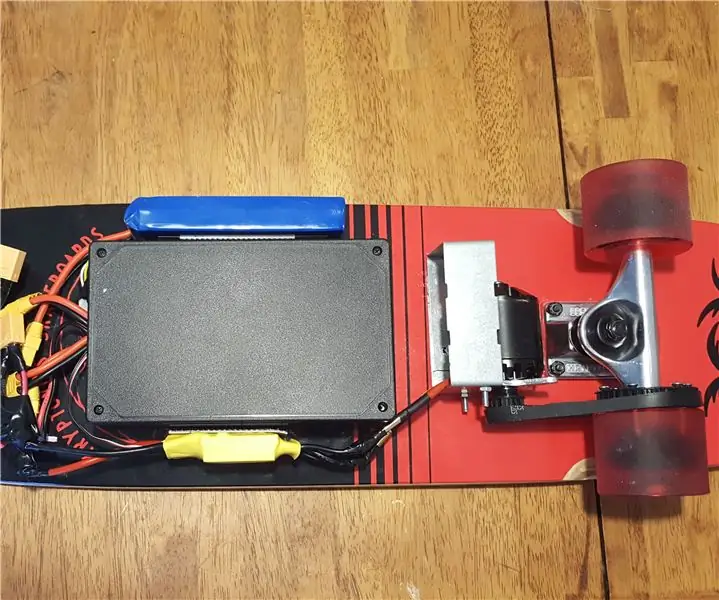
Električna rolka, občutljiva na pritisk: Ta navodila so nastala v skladu s projektnimi zahtevami Makecourseja na Univerzi v Južni Floridi (www.makecourse.com). Naslednja navodila bodo razložila postopek izdelave električne rolke, ki uporablja pritisk
Diy električna rolka: 14 korakov (s slikami)
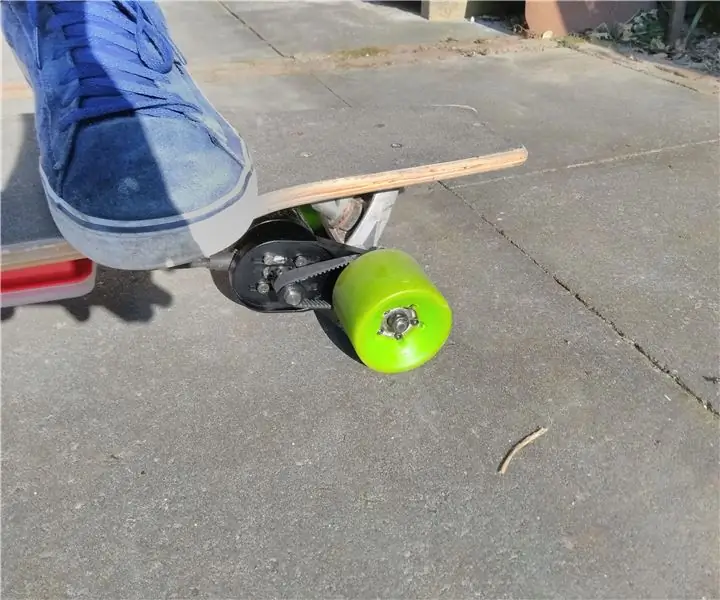
Diy Electric Skateboard: Po dveh letih raziskav sem zgradil svojo prvo električno drsalko. Izdelava lastne električne rolke je oblika